Mobile Factories For Schools
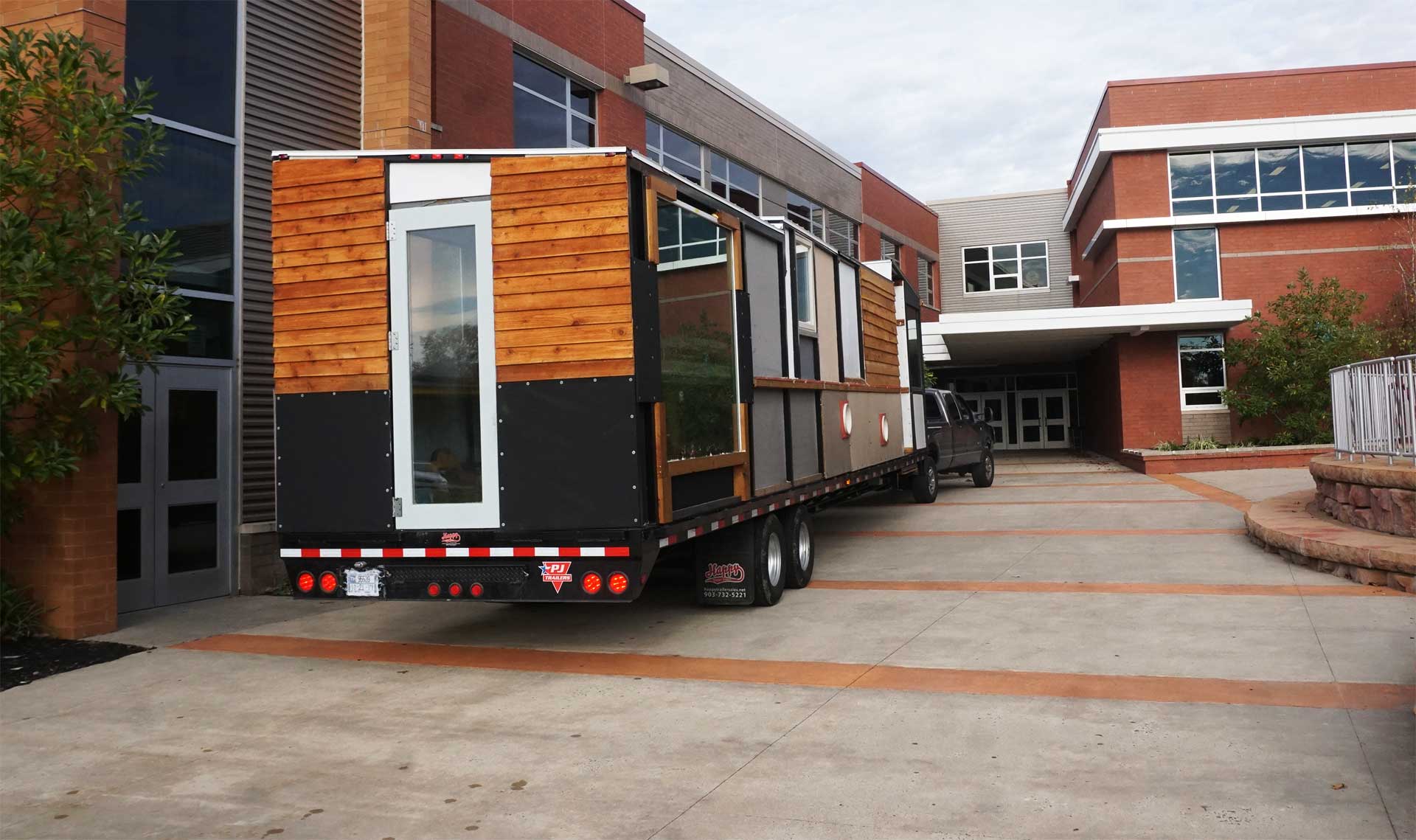
The foundation is a 40' flat-deck gooseneck commercial class trailer, built in Texas by PJ. On the flatbed we build out a trick enclosure designed to connect the students both to the manufacturing process and each other. When the trailer is parked at the base of a ski resort, in the forest or at the various schools within the district there is a stronger connection to the environment around. It is no longer a classroom. It's a bridge into the world of innovation, connectivity, collective effort, design, the list goes on. The point being; It's an incredible environment to learn the art of manufacturing.
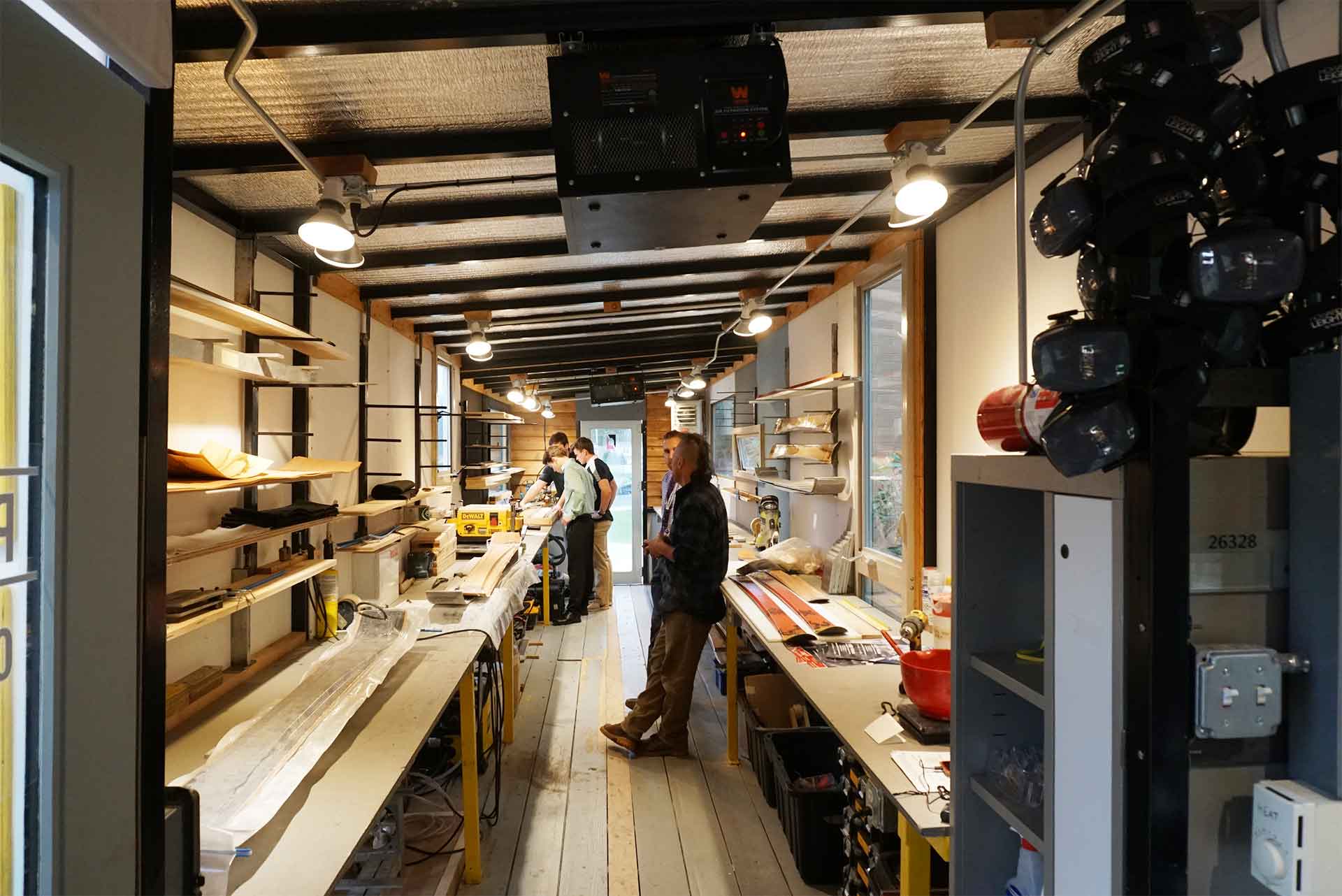
One of the purposes of good conversation is to give you direction. These students are self motivated. Need we say more?
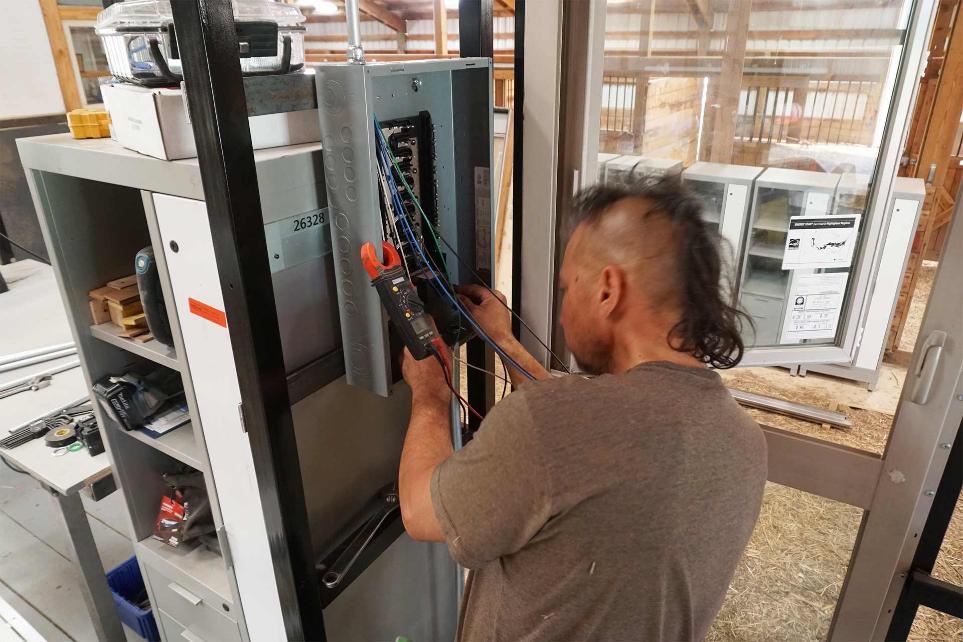
The factory envelope design/build is comprehensive. It includes structural, insulation, glazing, water mitigation, electrical, lighting, heating, safety & first aid, egress, weight distribution, DOT compliance, portable fire extinguisher compliance, manufacturing flow plan, showroom/office design, material storage, and other relevant aspects.
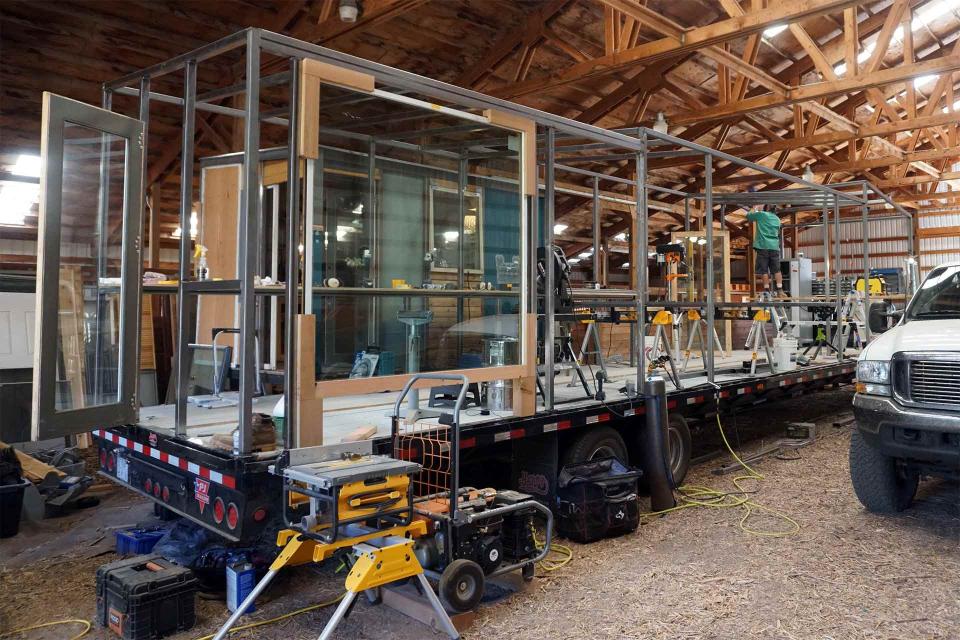
All of our glass is rated tempered safety or higher. We have an equivalent insulation rating of R-14 throughout the envelope. The gooseneck flatbed trailer is equipped with (2) 10,000lb Dexter Oil Bath Axils, 10-ply E Radial Tires, Powder Coated Pierce Beam Construction for low flat-deck height.
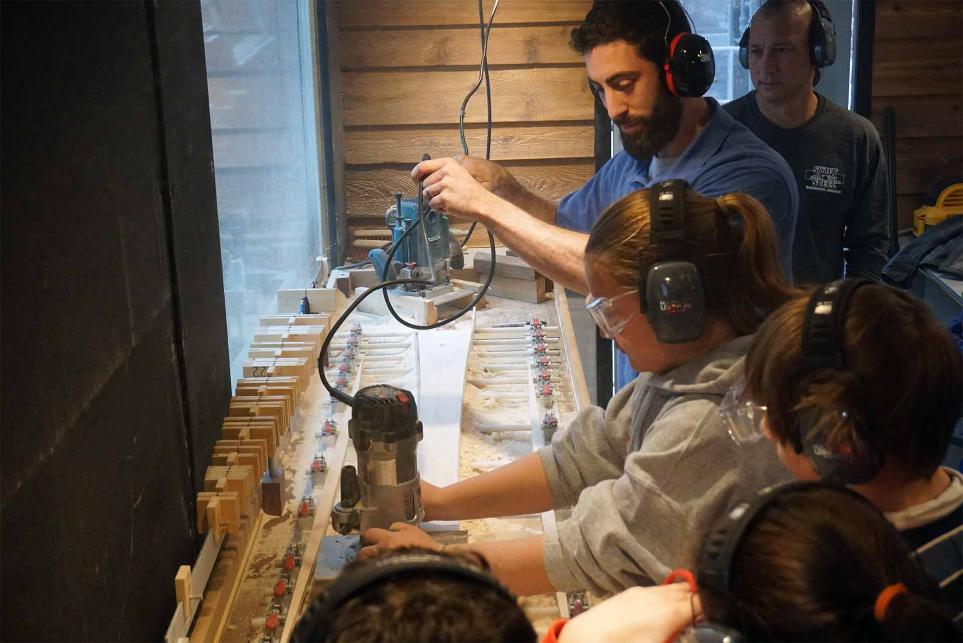
These are middle school students learning to work in pairs to safely manage the tools required to build the skis.
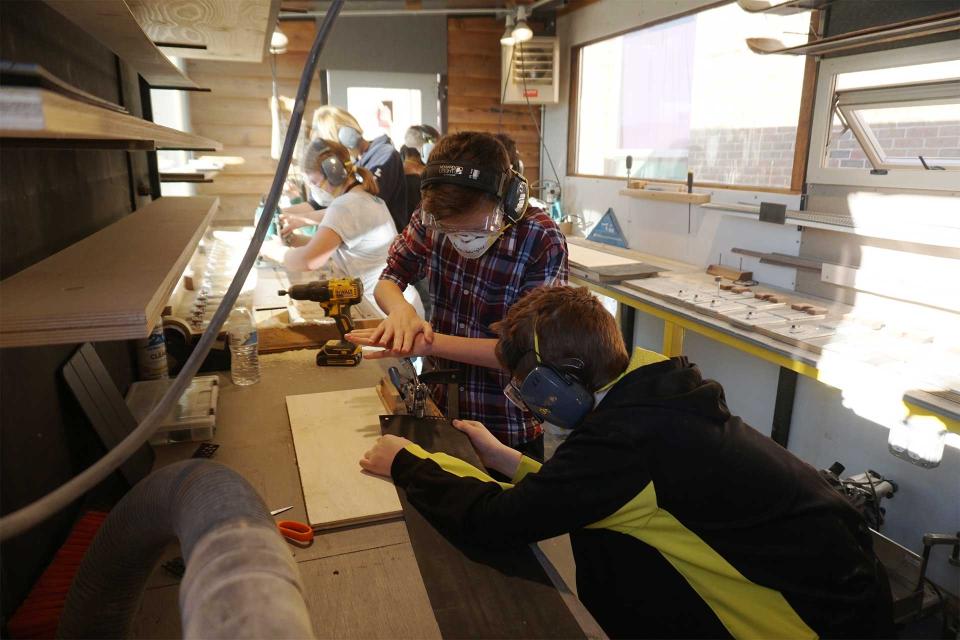
Class periods are relatively short in relation to the manufacturing processes. So we broke down the complete process into manageable units so a great deal can be accomplished during each class period.
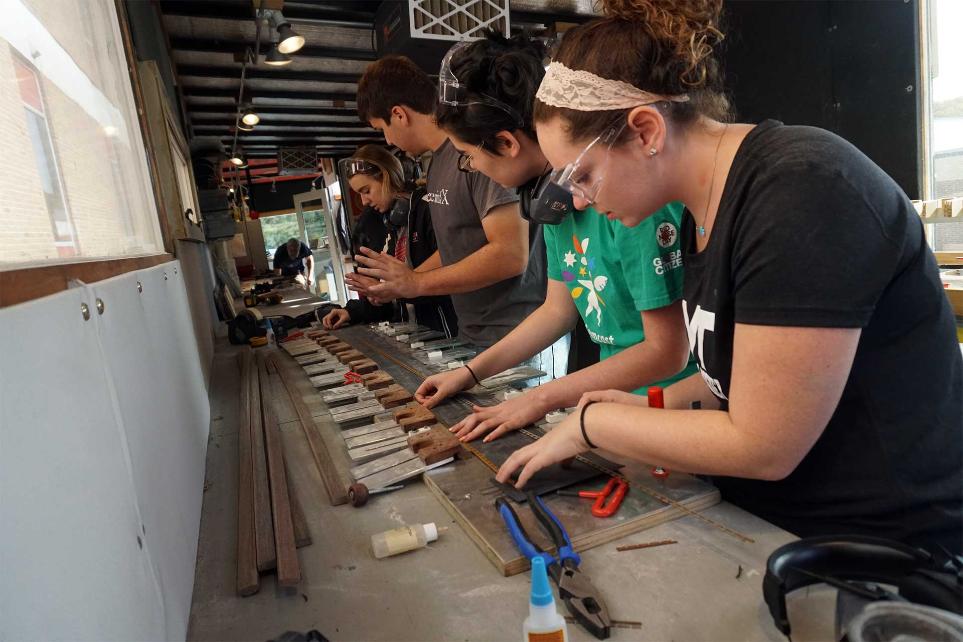
The key to scheduling is teaching a pair of students both safety and principals for their work station. This enables them to teach each rotating set of students, to learn from each other and also develop core competence in the workstation they've chosen. When all is said and done, every student has contributed to every other students finished skis.
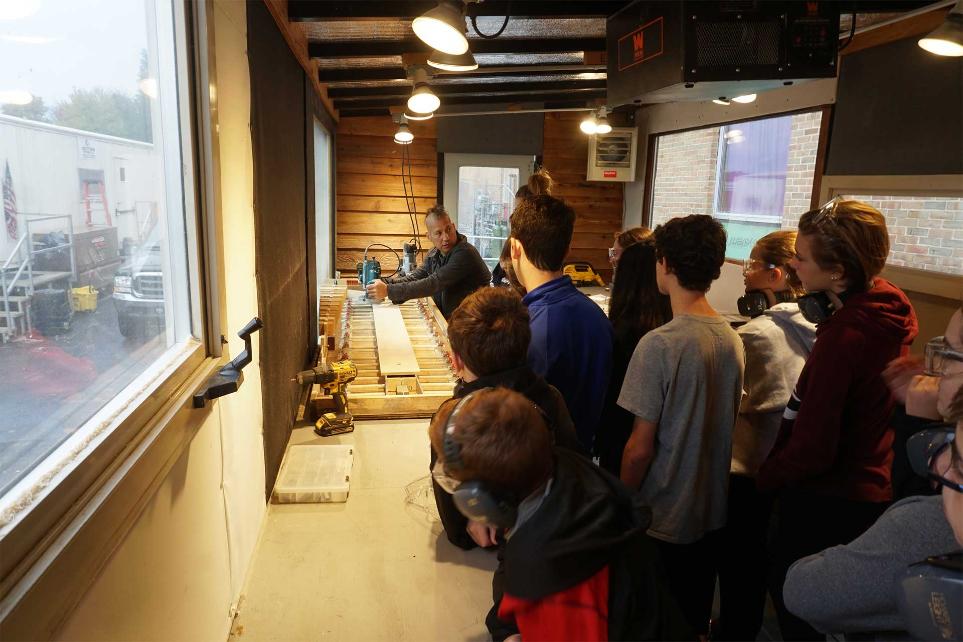
Part of the general conversation we have with the whole group is production safety. We make it relevant to getting the job done and it helps that they really want to get the job done.
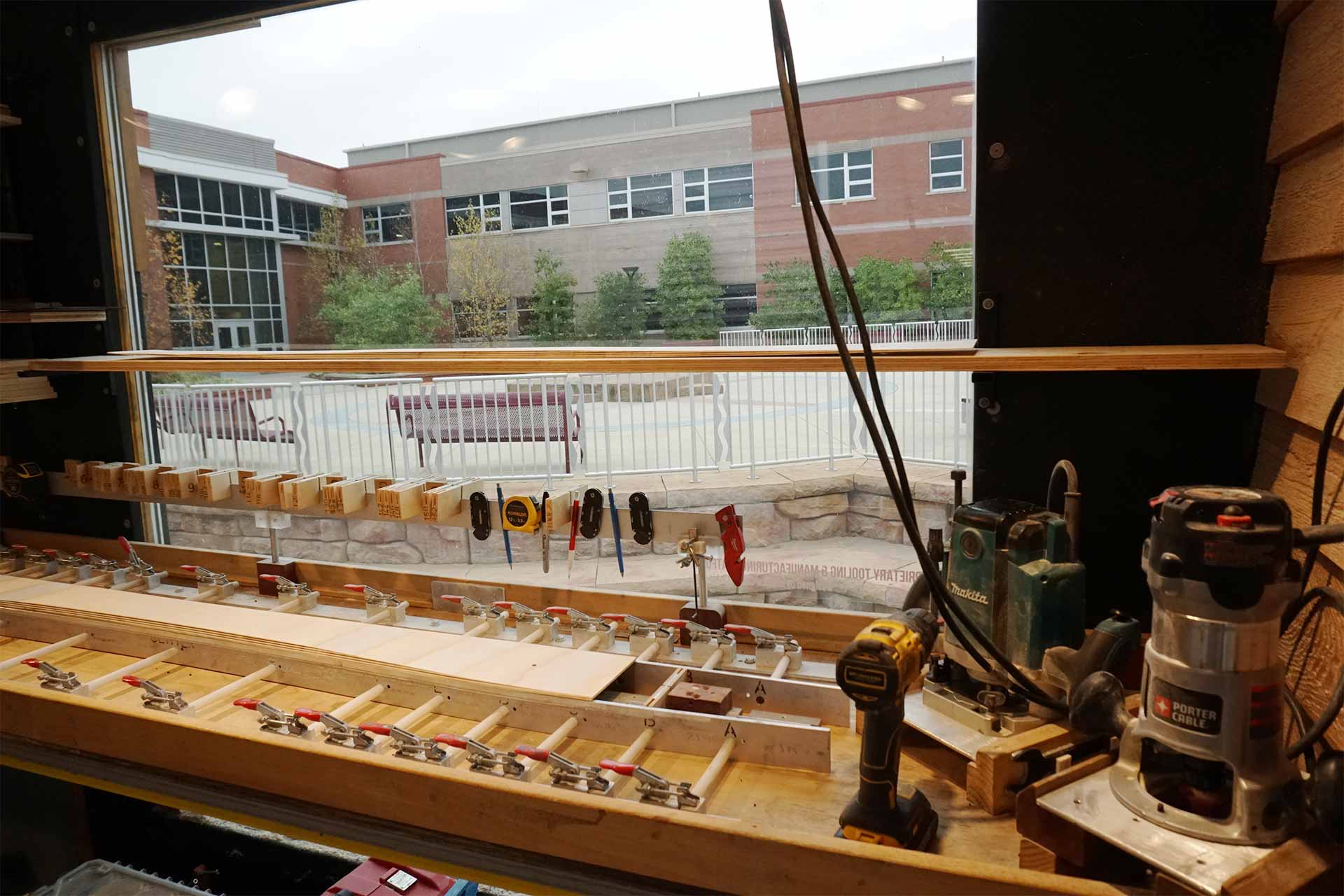
A key to production efficiency is tool and material storage. Students naturally put the tools back in their place and work in an organized environment. All of which helps us avoid chaos. Keep in mind that these manufacturing platforms reach speeds up to 65mph and must arrive safely and intact to the production site.
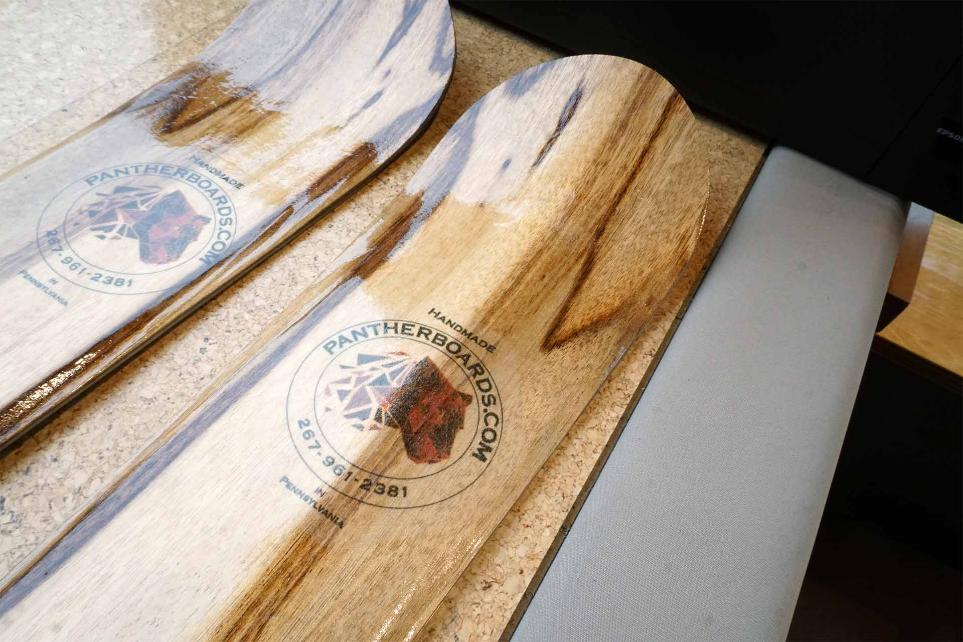
When students build market competitive skis & snowboards they have just taken one giant step forward to becoming entrepreneurs, business owners, and possibly more dedicated to the educational opportunities that lay before them. At the end of the day, what we've been trying to do is make education relevant.
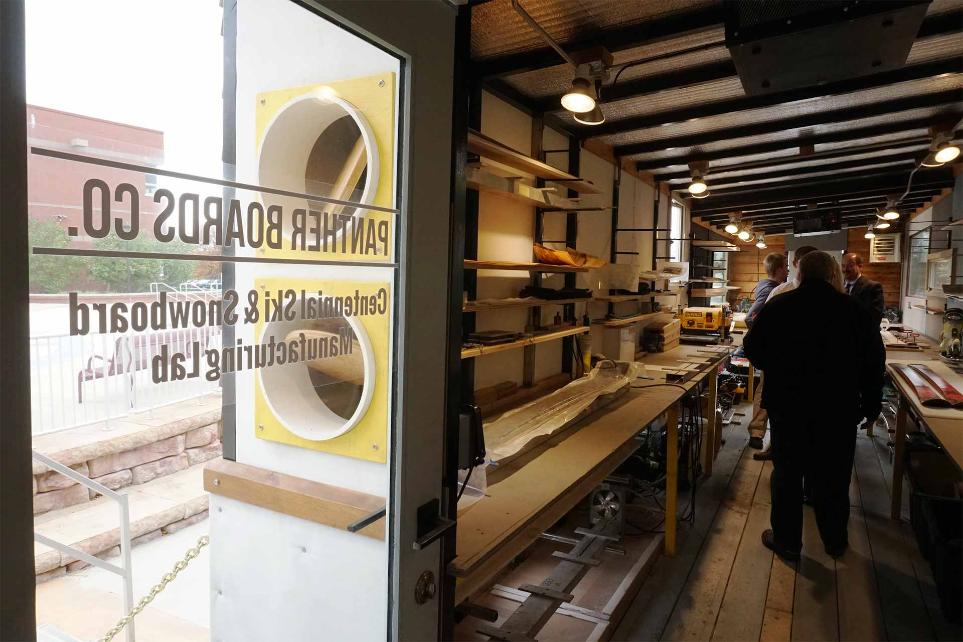
Whatever direction a high school chooses to take: Whether it be an after-school business program with a focus on manufacturing high performance skis & snowboards for the public, or places a focus on engineering and material sciences, or creates intersections for ski design and the graphic arts, or prototype development to go beyond the cutting edge, or curriculum that dives deep into business management, supply chain management, or students teaching adult education, where they oversee Build-Your-Own-Ski Workshops for the general public, we are here to provide our insights.
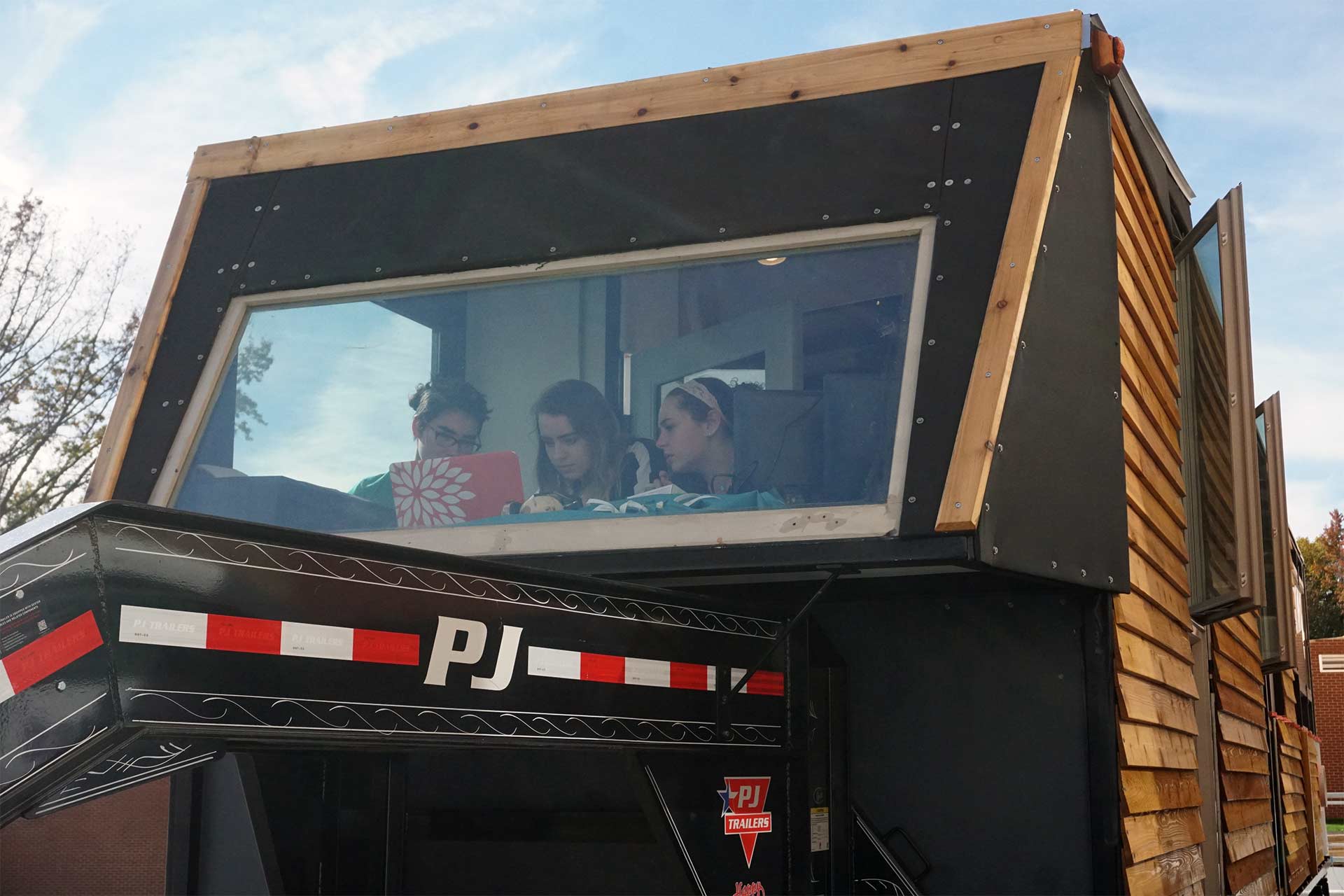
We take note of how students occupy space. We design accordingly.
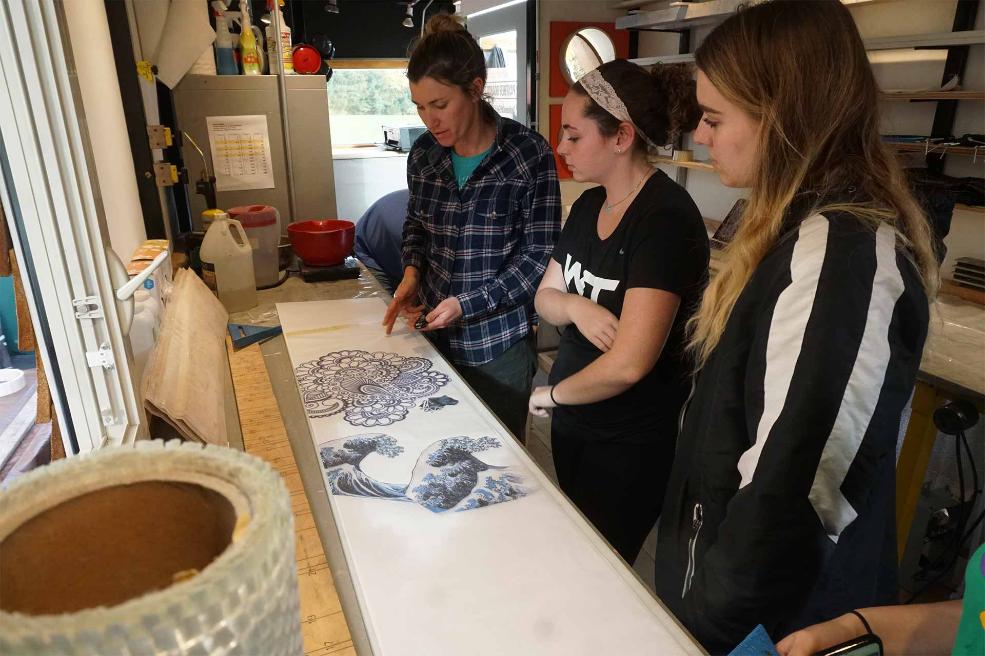
When students design their own graphics, it allows them an avenue of expression. It's their design. It's what they want their skis & snowboards to look like. This level of influence and creativity is rather empowering.
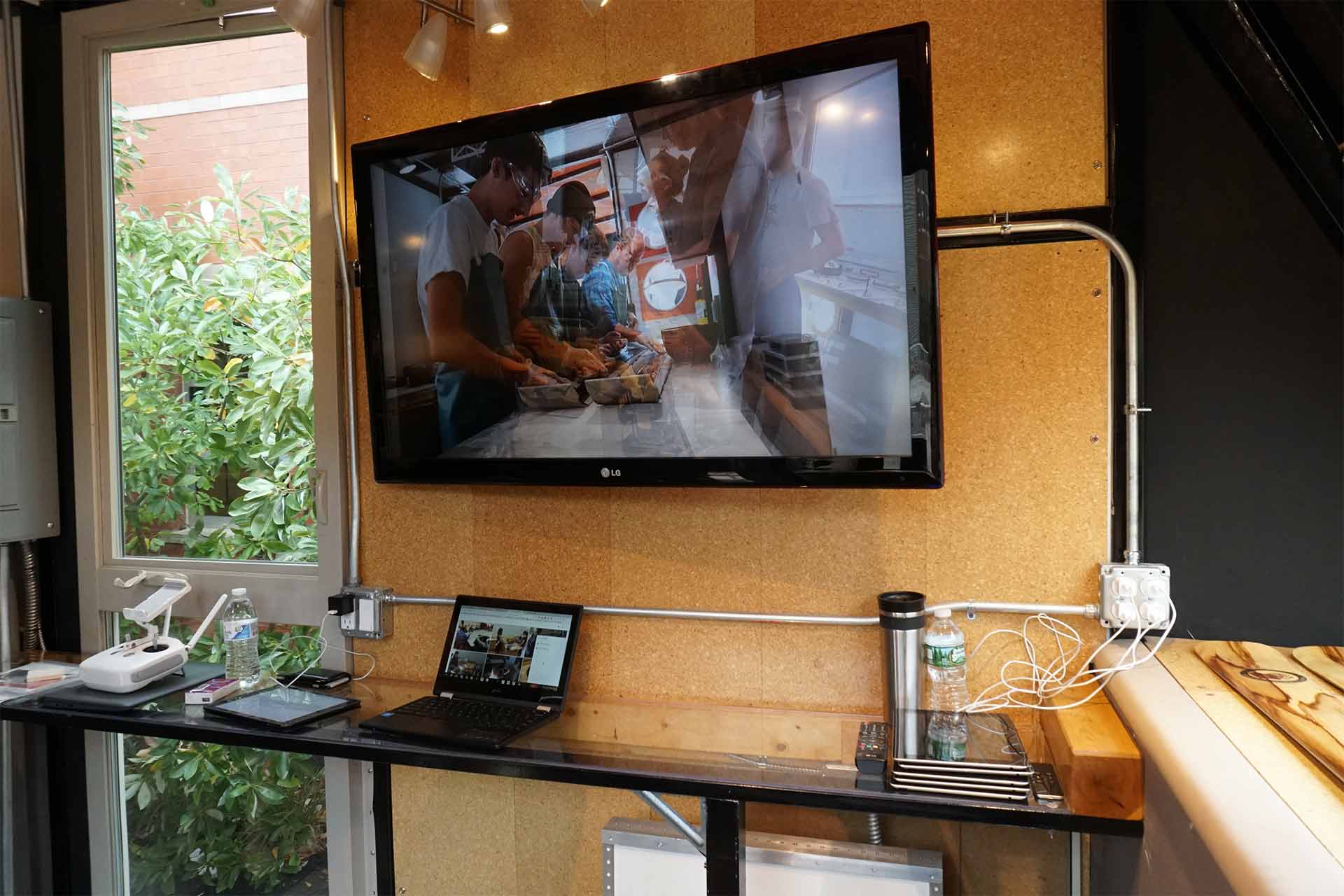
Creating the interior showroom space allows visitors to come on board and hear, see and experience manufacturing in America first hand.
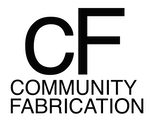
© Copyright 2020 Community Fabrication, LLC